A furniture maker in Wales has branched out into wooden bikes. Can his creations put the wheels in motion for a cycling revolution?
Booming bicycle sales and a revived zeal for slower, less impactful travel are among the pandemic’s silver linings. But as demand for bikes outstrips the supply of raw materials, many big-name manufacturers fear that their sprint start risks sputtering to an ignominious halt.
Not so Twmpa Cycles, based in Hay-on-Wye at the foot of the Black Mountains in the Welsh borderlands. Eschewing traditionally used materials like carbon fibre, steel and aluminium, Twmpa make their bike frames from wood. Specifically, British-grown ash.
In doing so, they’re not only creating a quirky talking point, but are also starting a conversation about the sustainability of bicycle manufacturing.
“It’s great to push for more bikes and fewer cars on the road,” says company founder Andy Dix, “but you can’t escape the fact that the bike industry as a whole is pretty energy intensive.”
Minimising environmental impact is something Dix has always strived for in his work. “Rather than relying on processed metals, or layers of plastic that will one day end up in landfill, I’m building bikes from captured carbon, in a process powered by sunlight,” he explains.
Cardiff-born Dix spent 17 years honing his skills as a furniture maker. In his downtime, the weather-beaten moors and shattered sandstone bridleways of the Brecon Beacons proved the ideal playground for mountain bike adventures from his base in Hay.
The idea for Twmpa Cycles – named after one of the Black Mountains peaks – was sown in conversation with author Rob Penn, also an avid cyclist, at the Hay Festival. Penn was commissioning craftspeople to make items from a felled ash tree, for his book: The Man Who Made Things Out of Trees. Dix’s restless inventive streak dovetailed perfectly.
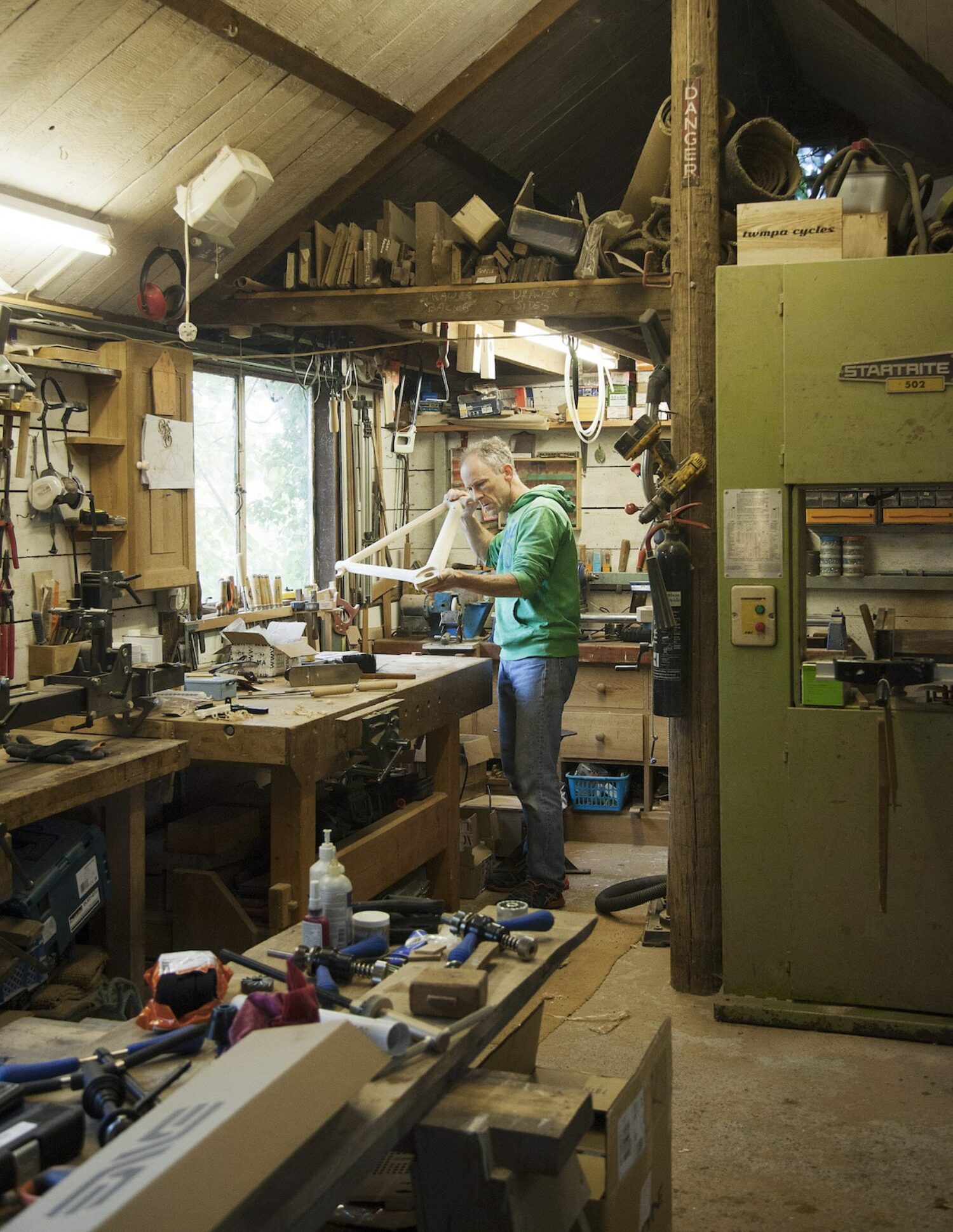
Dix examines a frame in his Black Mountains workshop. Image: Mark Griffiths
“We talked about what I might build, and I suggested a bike,” Dix explains. “It seemed like a good fit, but actually I had no experience in bike building, and Rob had a publishing deadline. In the end, I built him a writing desk instead.”
But the seed had been planted. “The more I thought about it, the more I knew I had to make it happen – purely to see if I could,” says Dix.
He spent two years building his first prototype. Seeking out the roughest roads for test rides, he found the bike strikingly comfortable, and – with a little research – discovered what manufacturers of wooden-handled tools have known for centuries.
“Ash is a kind of underdog: relatively cheap and fairly easy to process,” Dix says. “It’s a very utilitarian material, but it turns out it’s also brilliant at absorbing vibration. I was gliding along battered roads that would have shaken me to bits on a carbon bike. The penny dropped: not only could I make a bike out of wood, but it had inherent advantages over other materials.”
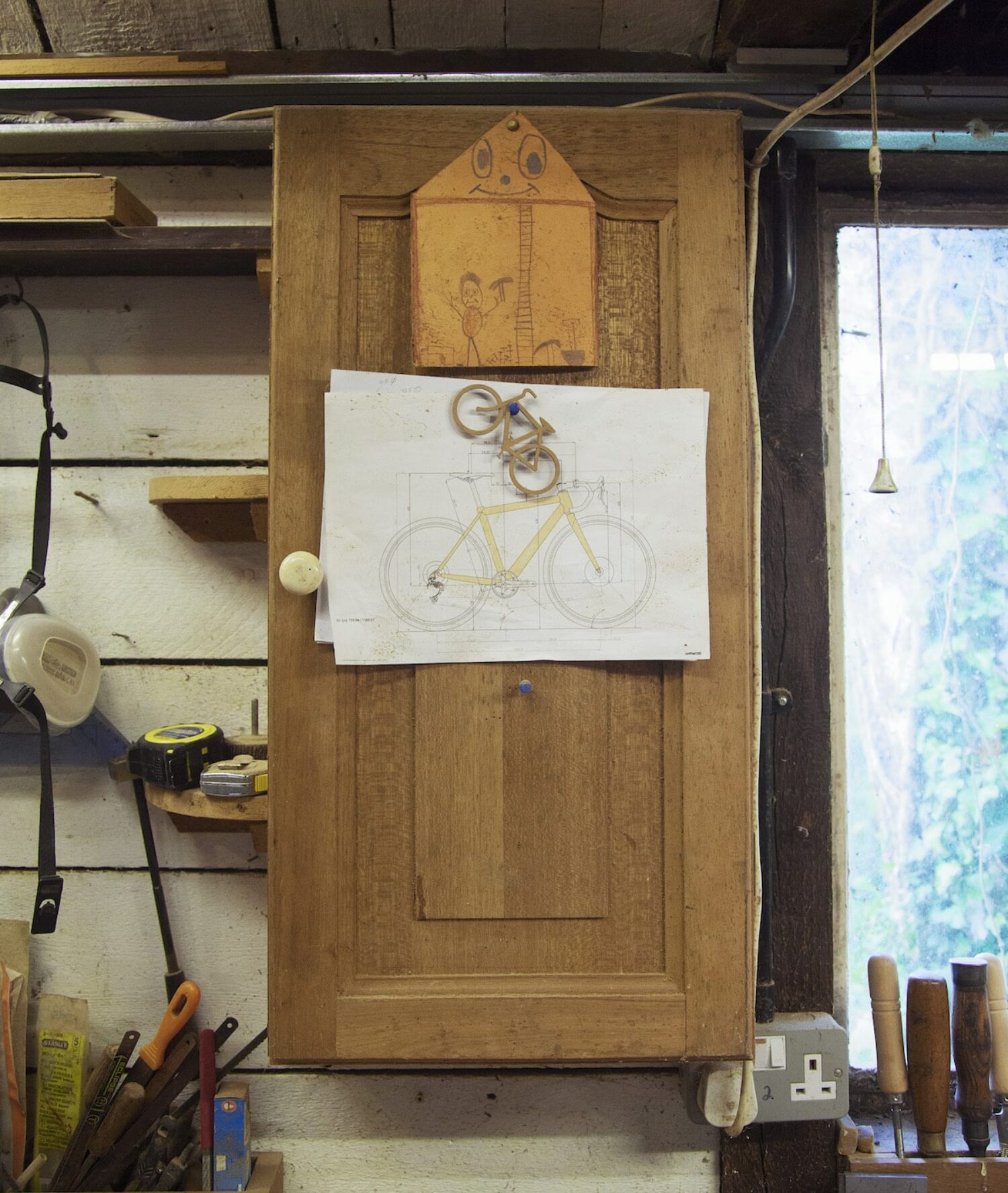
‘Stand out, ride hard, and turn heads,’ goes Twmpa’s mantra. Image: Mark Griffiths
Interest in Dix’s prototype from other cyclists prompted him to explore ways of streamlining the production process. He joined forces with Cardiff Metropolitan University’s FabLab, to marry his skills with digital design and manufacturing.
He now selects ash planks from a local sawmill, before joining them by hand. Planks are shaped and hollowed by computer-controlled machinery to create the bicycle’s familiar front triangle. Dix adds the other frame elements in his workshop.
To the doubters, who may be concerned about the durability of a bike made from ash, Dix is quick to point out that wood has a better weight- to-strength ratio than steel or aluminium. He’s clocked up more than 3,000 miles on his own wooden bike, “riding it hard in the mountains and on routes it’s really not designed for”, and has had a frame subjected to fatigue tests, which simulate high impact crashes and a decade of riding.
“It passed with flying colours,” he notes.
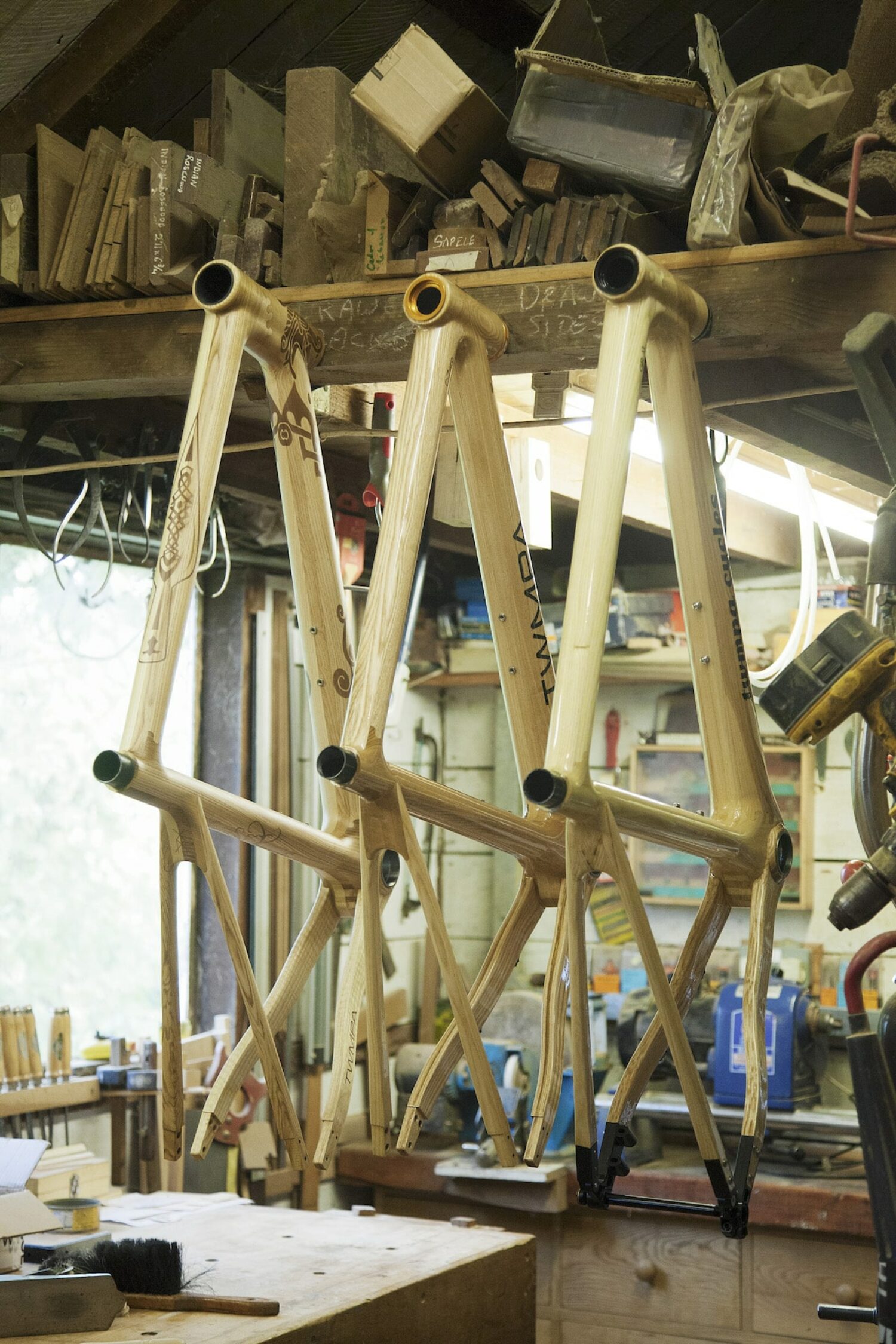
At £3,000 a frame, Twmpa bikes are beyond most budgets. Image: Mark Griffiths
Bicycle manufacturing has grappled with reconciling its energy-hungry production methods and weighty carbon footprints with the frequently green, sustainable ambitions of much of its core market.
One of the world’s largest brands, Specialized, partnered with Duke University in Durham, North Carolina, to develop an in-depth study into the environmental impact of the bike industry. They found that a year’s production of its Allez aluminium road bike frame generated as much CO2 as driving a petrol SUV for 15 million miles.
And while the industry is making inroads into carbon fibre recycling, as much as a third of the material is wasted in bike production processes, with reports of some manufacturing facilities dumping offcuts in the sea.
Says Dix: “The emissions figures are astonishing. Producing a tonne of planked wood emits minus 457kg of CO2 – in other words, wood locks carbon up. Manufacturing a tonne of aluminium emits 4,532kg.”

Wood has many advantages over other materials, reckons Dix. Image: Mark Griffiths
Cost is another consideration: a standard Twmpa frame starts at £3,000, placing it well beyond many people’s budgets.
Dix is also realistic about the contribution his fledgling business can make to reducing global carbon emissions, but believes the example set by Twmpa is a pedal stroke in the right direction.
Although Twmpa’s focus is currently on building gravel bikes – blurring the lines between on- and off-road adventures – Dix has plans for a city commuter, and is developing a wooden e-bike with Scottish startup FreeFlow Technologies.
“Our ancestors built amazing things out of wood, but it’s been usurped by more modern materials,” he says. “We have this incredibly sophisticated engineering material growing naturally all around us. It’s time people started to think about it in the same way as novel materials like carbon fibre.”
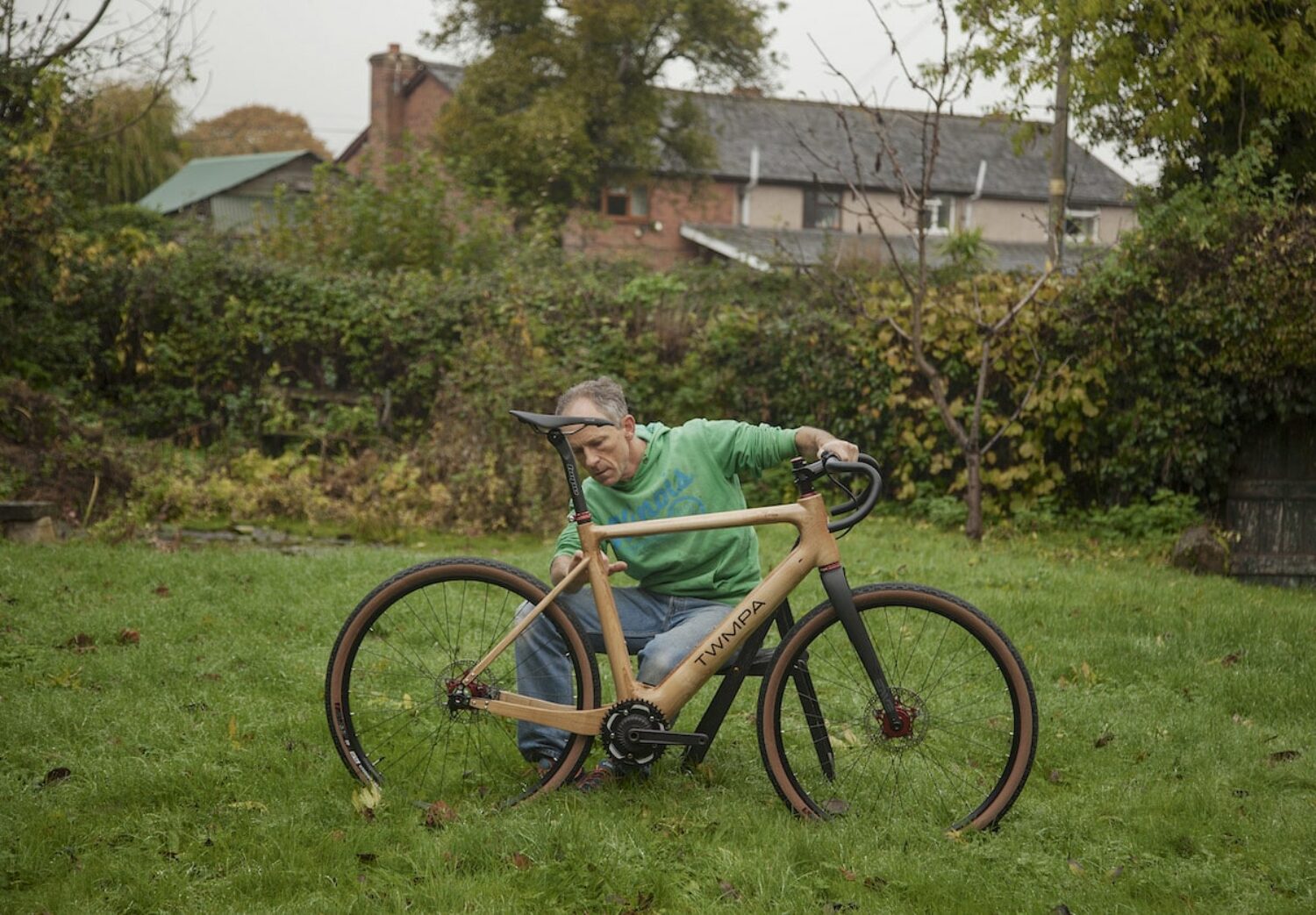
Dix is putting the wheels in motion for a wooden renaissance. Image: Mark Griffiths
On the other side of the Black Mountains, in Abergavenny, Rob Penn has already taken one of Twmpa’s bikes for a test ride.
“I was dubious,” admits the author, who wrote and presented the TV documentary Ride of my Life: The Story of the Bicycle. “But having ridden one, I’m going to steal food from my children’s mouths until I can afford one.”
Penn, who is patron of the Small Woods Association, has also been a vocal advocate of the Stump Up For Trees campaign, which aims to plant a million trees in the Brecon Beacons.
“There’s a global swing back towards tree planting as a means of mitigating climate change,” he says. “But there’s no point in planting trees if we’re not going to use the wood to lock up carbon for a very long time.
“Making better use of wood at the back end of a tree’s life is totally fundamental to mitigating climate change – and what better way to do that than in a bicycle?”
Main image: Mark Griffiths